Article Summary:
This comprehensive guide covers modern ferrosilicon production technologies, quality control methods, industrial applications, and market analysis for 2025.
Essential resource for metallurgical engineers and steel industry professionals.
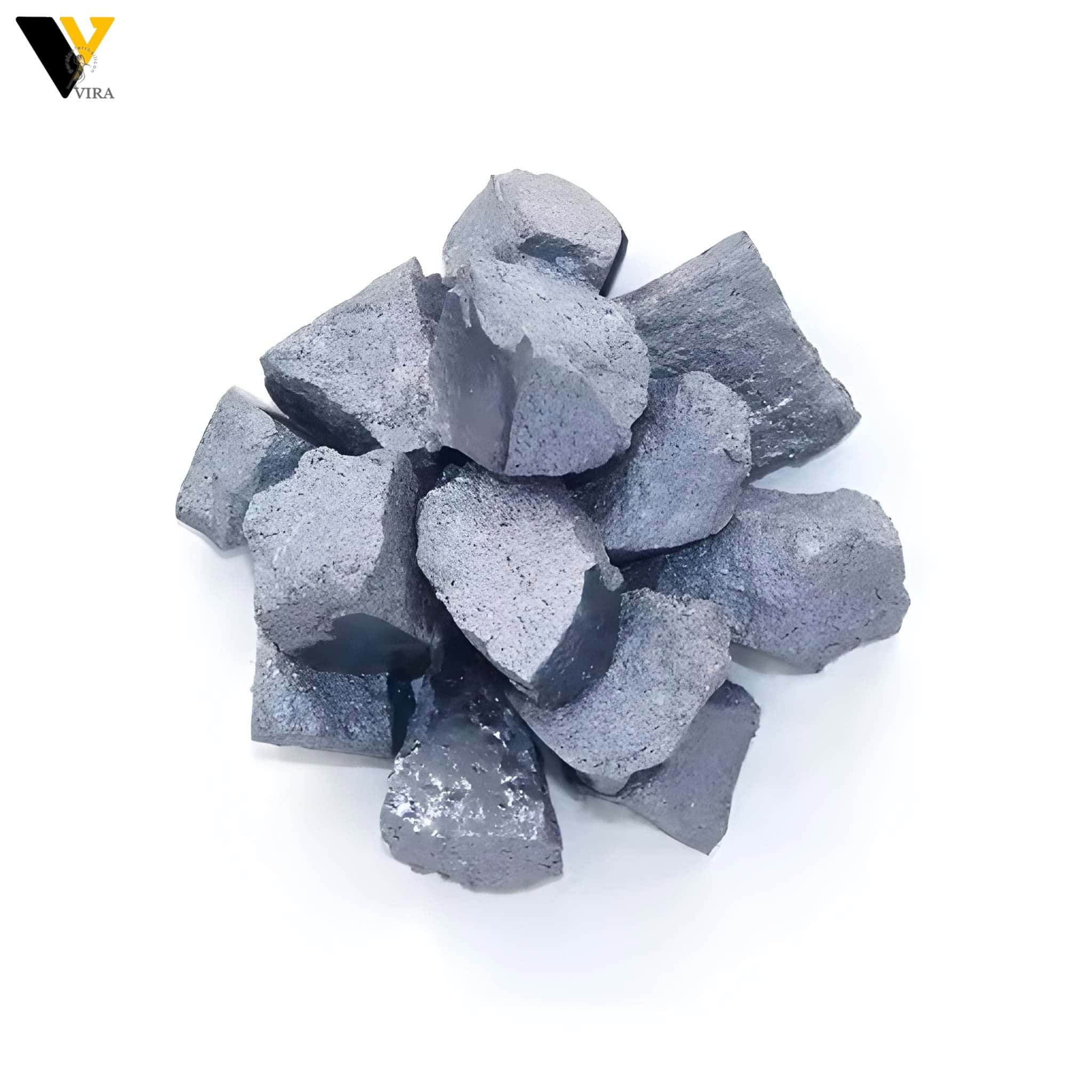
Introduction to Ferrosilicon:
Ferrosilicon is a crucial ferro-alloy containing iron and silicon, primarily used as a deoxidizer and alloying agent in steel production.
With silicon content ranging from 15% to 90%, ferrosilicon plays an essential role in modern metallurgy.
Key Properties:
🧪Chemical Composition: Fe-Si alloy
🔧Melting Point: 1200°C – 1250°C
🔩Density: 6.7-7.1 g/cm³
⚙️Primary Use: Steel deoxidation
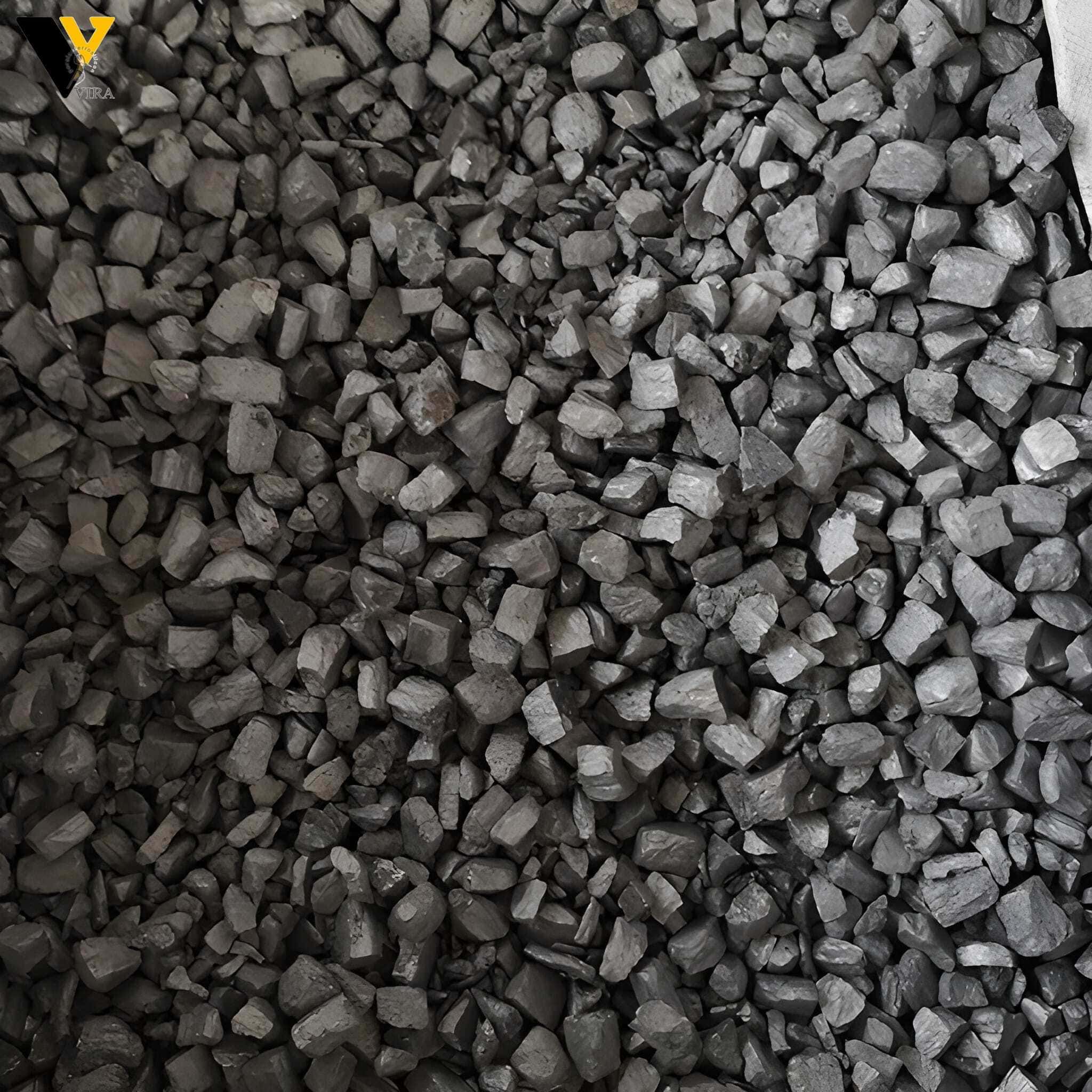
Production Methods:
1. Submerged Arc Furnace Method:
The most common industrial production method using electric arc furnaces:
Parameter | Specification |
Temperature | 1800-2000°C |
Power Consumption | 8000-9000 kWh/ton |
Raw Materials | Quartz, Coke, Iron ore |
Production Capacity | 50-200 tons/day |
Process Steps:
- Raw material preparation and sizing
- Charging into submerged arc furnace
- Electric arc melting at high temperature
- Tapping and casting
- Crushing and screening
2. Plasma Arc Furnace Technology:
Advanced method for high-purity ferrosilicon:
Advantage | Description |
Energy Efficiency | 20% less power consumption |
Product Purity | Higher silicon recovery |
Environmental Impact | Reduced emissions |
Process Control | Better temperature management |
3. Induction Furnace Method:
Suitable for small-scale production:
Benefits:
- Precise temperature control
- Lower investment cost
- Flexible production capacity
- Better working environment
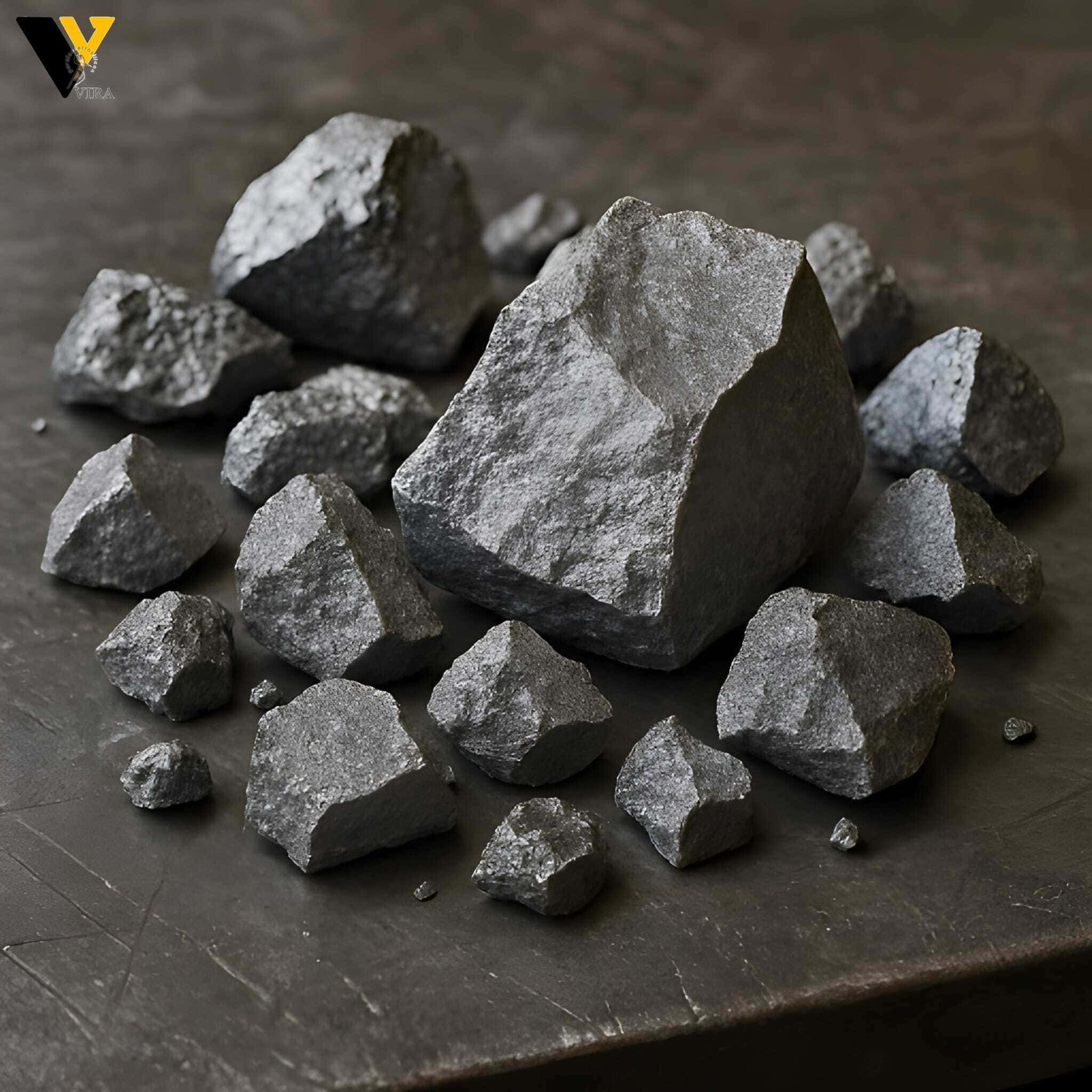
Quality Standards:
International Standards Comparison
Standard | Si Content (%) | C Content (%) Al |
ASTM A100 | 75.0 min | 0.2 max |
JIS G2302 | 75.0 min | 0.15 max |
GB/T 2272 | 75.0 min | 0.2 max |
EN 10343 | 75.0 min | 0.2 max |
Quality Control Parameters:
Test Parameter | Method | Frequency |
Chemical Analysis | XRF Spectroscopy | Every batch |
Size Distribution | Sieve Analysis | Daily |
Moisture Content | Gravimetric | Shiftbasis |
Density | Pycnometer | Weekly |
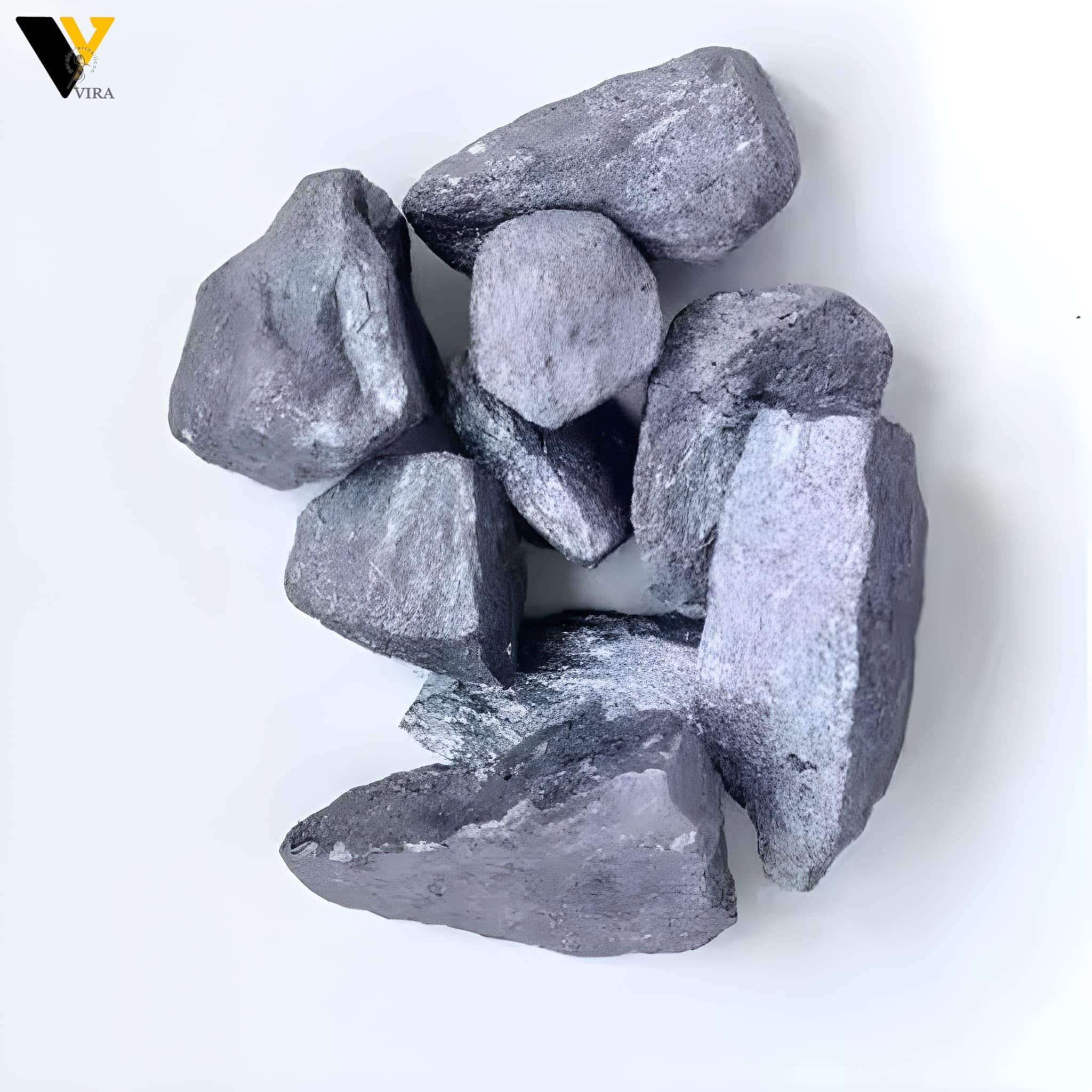
Industrial Applications:
Steel Industry Applications
Application | Si Content (%) | Usage Rate |
Carbon Steel Deoxidation | 75-78 | 2-4 kg/ton |
Alloy Steel Production | 65-75 | 5-8 kg/ton |
Cast Iron Production | 45-65 | 8-12 kg/ton |
Stainless Steel | 70-75 | 3-6 kg/ton |
Other Industrial Uses:
- Aluminum Industry: Silicon source for aluminum alloys
- Chemical Industry: Silicon tetrachloride production
- Solar Industry: High-purity silicon manufacturing
- Refractory Industry: Silicon carbide production
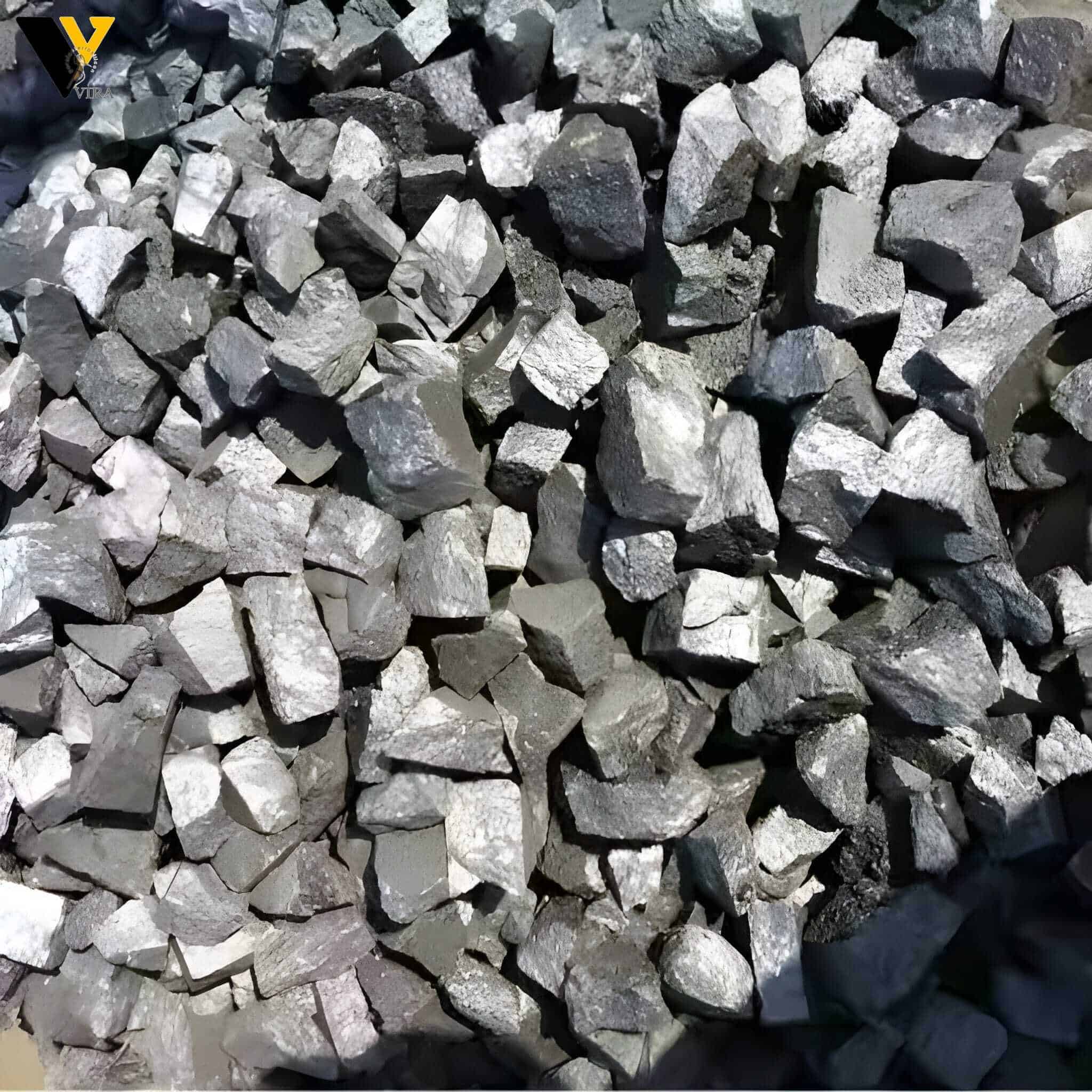
Market Analysis 2025:
Global Production Statistics
Country | Production (Million Tons) | Market Share (%) |
China | 4.2 | 65% |
Russia | 0.8 | 12% |
IRAN | 0.3 | 5% |
Brazil | 0.2 | 3% |
Others | 1.0 | 15% |
Price Trends 2025
Grade | Q1 2025 ($/MT) | Forecast Trend |
FeSi 75% | 1,450-1,550 | Stable |
FeSi 65 | % 1,200-1,300 | Slight increase |
FeSi 45% | 950-1,050 | Moderate growth |
Market Drivers
- Steel industry growth in developing countries
- Infrastructure development projects
- Automotive industry expansion
- Green steel production initiatives
Frequently Asked Questions:
Q1: What is the difference between FeSi 75% and FeSi 65%?
A: FeSi 75% contains 75-80% silicon and is primarily used for steel deoxidation, while FeSi 65% contains 65-72% silicon and is used for both deoxidation and alloying purposes.
Q2: How is ferrosilicon quality measured?
A: Quality is measured by silicon content, carbon content, aluminum content, phosphorus levels, and size distribution according to international standards like ASTM A100.
Q3: What are the main raw materials for ferrosilicon production?
A: The primary raw materials are quartz (SiO₂), coke or coal (carbon source), iron ore or steel scrap, and wood chips for specific grades.
Q4: Why is ferrosilicon important in steel production?
A: Ferrosilicon acts as a deoxidizer, removing oxygen from molten steel, and as an alloying agent to improve steel properties like strength and corrosion resistance.
Q5: How does ferrosilicon particle size affect its performance?
A: Smaller particles provide faster dissolution and better distribution in molten steel, while larger particles are more cost-effective for bulk applications.
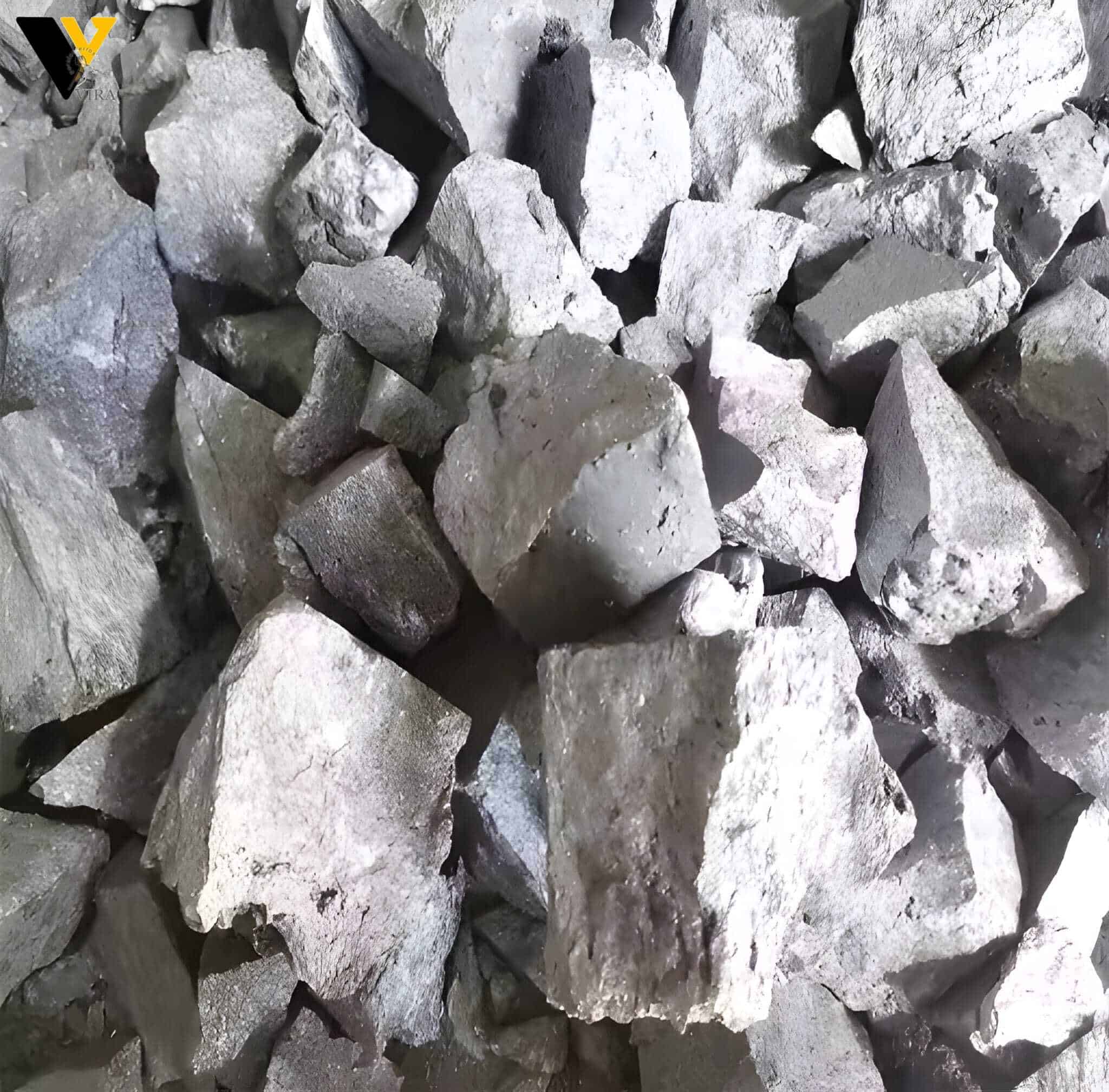
Conclusion:
Ferrosilicon remains a critical component in modern steel production, with evolving technologies improving both efficiency and environmental sustainability.
The 2025 market shows steady growth driven by global infrastructure development and automotive industry expansion.
Key Takeaways:
- Submerged arc furnace method dominates industrial production
- Quality standards are becoming more stringent globally
- Environmental regulations are driving technological innovations
- Asian markets continue to lead production and consumption
- Future growth depends on green steel initiatives and renewable energy adoption
Industry Outlook:
The ferrosilicon industry is transitioning toward more sustainable production methods, with increased focus on energy efficiency and carbon footprint reduction.
Companies investing in advanced technologies and environmental compliance will maintain competitive advantages in the evolving market landscape.